摘要:某Q345D输送流体用无缝钢管在工作过程中突然发生爆裂,通过化学成分分析、拉伸试验、冲击性能测试和断口SEM扫描电镜分析等方法,对无缝钢管的断裂原因进行分析。结果表明该无缝钢管的化学成分满足要求,但钢管长期处于高温条件下运行,发现裂口处碳化物析出,碳化物颗粒周边碳含量降低,基体强度和冲击性能随之下降,在高温蒸汽和化学气体的长期作用下内表面被腐蚀的基体处和碳化物颗粒处首先萌生裂纹,随着裂纹的扩展,最终发生爆裂。 关键字:无缝钢管;强度;冲击性能;腐蚀;爆裂 引言 输送流体用无缝钢管用于管输送石油、天然气、煤气、化学气体和水等,这就要求钢管具有高的抗氧化性能和耐腐蚀性能,并有良好的组织稳定性和耐持久强度。某Q345D输送流体用无缝钢管在工作3年后局部发生爆裂,为了找出无缝钢管爆裂原因,避免类似事故再发生,笔者对该无缝钢管进行检验和分析。 1理化检验 1.1化学成分分析 使用Spark直读光谱仪进行化学成分分析,检测结果见表1,可见该无缝钢管的化学成分符合GB/T 8163-2018《输送流体用无缝钢管》对Q345D钢管化学成分的规定。 表1爆裂钢管的化学成分检测结果(质量分数 %) 项目 | C | Si | Mn | P | S | Nb | V | Ti | Cr | Ni | 实测值 | 0.14 | 0.28 | 1.32 | 0.016 | 0.008 | 0.01 | 0.02 | 0.04 | 0.11 | 0.02 | 标准值 | ≤0.18 | ≤0.50 | ≤1.70 | ≤0.030 | ≤0.025 | ≤0.20 | ≤0.25 | ≤0.25 | ≤0.15 | ≤0.08 | 1.2冲击性能测试 依据GB/T 229-2007《金属材料夏比摆锤冲击试验方法》,采用JBS-300数显金属冲击试验机进行冲击性能检测,在爆裂钢管的裂口上端、下端和裂口处分别截取3组冲击样品进行检测,每组样品测3个冲击值。由于该钢管的厚度为7mm,无法制备标准样品,按GB/T 8163-2018《输送流体用无缝钢管》的要求制备小试样,冲击试验样品尺寸为5mm×10mm×55mm,试验温度为-20℃,V型缺口冲击吸收功KV2标准值按递减系数0.5计算为10J。检测结果见表2,可见爆裂钢管的冲击性能均满足GB/T 8163-2018《输送流体用无缝钢管》的要求,但裂口处的冲击吸收功明显小于裂口的上下端部位。 表2开裂钢管的维氏硬度检测结果 样品位置 | 检测结果 | 裂口上端 | 40.4,46.5,43.4 | 裂口下端 | 38.9,42.5,39.6 | 裂口处 | 20.4,18.8,22.5 | 标准值 | ≥10J | 1.3拉伸性能分析 在爆裂钢管上截取3根拉伸试验样,取样位置为裂口的上端、下端和裂口处,分别标识为样品1、样品2和样品3。根据GB/T 228.1-2010《金属材料 拉伸试验 第1部分:室温试验方法》进行检测,检测结果见表3,可见样品1和样品2试验样的抗拉强度均满足GB/T 8163-2018《输送流体用无缝钢管》的要求,而样品3抗拉强度明显不足。 表3开裂钢管拉伸性能检测结果 样品标识 | 屈服强度Rp0.2/ MPa | 抗拉强度Rm/ MPa | 断后伸长率A/% | 样品1 | 378 | 556 | 26.5 | 样品2 | 380 | 562 | 26.0 | 样品3 | 未见屈服 | 323 | 8.5 | 标准值 | ≥345 | 470~630 | ≥20 | 1.4SEM扫描电镜分析 使用蔡司扫描电镜对开裂钢管的外表面、内表面和断面形貌进行分析。如图1可见,爆裂钢管的外表面和内表面有明显的龟裂裂纹,同时钢管的外表面和内表面都覆盖一层红褐色的锈垢,使用EDS能谱分析仪对锈垢进行分析,可知外表面和内表面的锈垢主要成分含量为氧和铁,还有少量的硅、钙、氢等元素,能谱分析结果见表4。  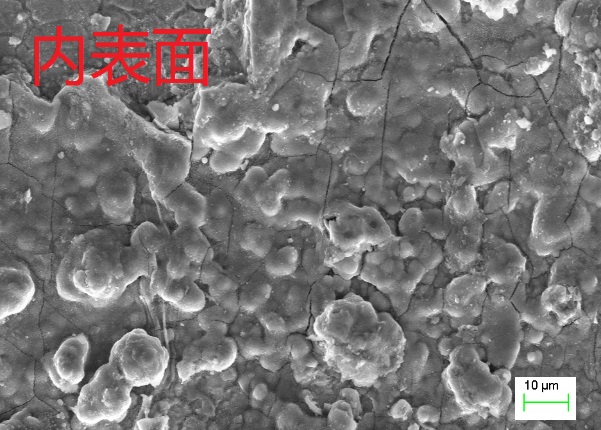
图1开裂钢管的外表面和内表面扫描电镜图 表4开裂钢管的外表面和内表面能谱分析结果(质量分数%) 位置 | O | Fe | Si | Ca | H | 外表面 | 32.22 | 42.15 | 3.66 | 2.78 | 1.78 | 内表面 | 33.87 | 43.02 | 2.23 | 1.56 | 2.43 | 如图2可见,爆裂钢管的断面有明显的非金属夹杂物颗粒,使用EDS能谱分析仪对夹杂物颗粒进行分析,发现碳含量较高,为碳化物颗粒,能谱分析结果见表5。 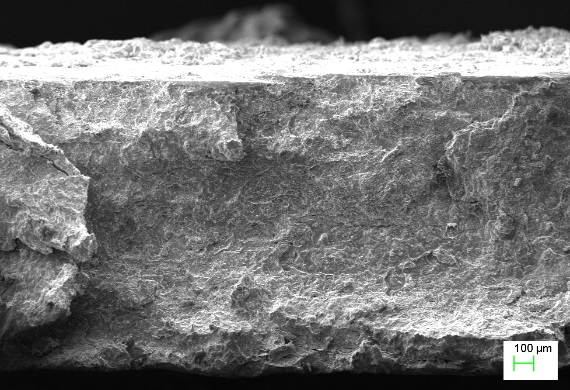 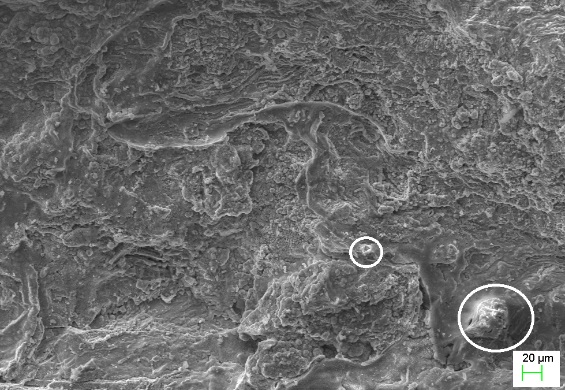
图2开裂钢管的断面扫描电镜图 表5夹杂物颗粒能谱分析结果(质量分数%) 项目 | C | Fe | Si | Ca | Cr | Ni | 实测值 | 22.54 | 41.69 | 7.89 | 8.67 | 2.16 | 1.68 | 2分析讨论 由化学成分检测结果可知,该爆裂钢管化学成分符合GB/T 8163-2018《输送流体用无缝钢管》的要求,但裂口处的抗拉强度不满足标准要求,裂口处的冲击性能虽然满足标准要求,但冲击吸收功明显小于裂口的上下端部位。从爆裂钢管SEM扫描电镜和EDS能谱分析可知,该钢管的外表面和内表面有明显的龟裂裂纹,说明钢管长时间在高温条件下运行,局部已经开始出现老化,爆裂钢管的外表面和内表面均覆盖一层红褐色铁锈,使用EDS能谱分析仪对锈垢进行分析,可知外表面和内表面的锈垢主要成分含量为氧和铁,还有少量的硅、钙和氢等元素,主要是钢管常年暴露在大气中氧化腐蚀和输送高温蒸汽和化学气体所形成的氧化铁铁锈[1]。断面处有明显的碳化物颗粒析出,是由于管道在高温蒸汽输送过程中形成的碳化物析出相,碳化物的聚集造成碳化物颗粒周边基体的碳含量降低,基体的强度也随之下降。同时碳化物的聚集又会导致应力集中,加速裂纹的萌生和扩展。该输送流体用无缝钢管在高温蒸汽和化学气体的常年氧化腐蚀下,裂口处内表面形成大量的氧化物[2],碳化物析出,基体碳含量逐步减少,钢管耐持久强度降低,而在高温蒸汽的热应力作用下,内表面被腐蚀的基体缺陷处和碳化物聚集区都可能首先萌生裂纹,随着基体强度的下降,加速裂纹的快速扩展,最终发生热应力腐蚀开裂。 3结论 造成Q345D输送流体用无缝钢管开裂的主要原因是该钢管长时间在高温蒸汽条件下运行,局部已逐步开始老化,碳化物的析出造成基体碳含量减少,强度不断降低,再加之高温蒸汽和化学气体的常年氧化腐蚀,在内表面被腐蚀的基体缺陷处和碳化物聚集区首先萌生裂纹,随着裂纹的扩展,最终发生热应力腐蚀开裂。 参考文献 [1]赵林松,等.某电厂锅炉高温过热器爆管原因分析[J].理化检验(物理分册)2019,55(3):214-217. [2]龙会国,等.T23钢管蒸汽侧氧化层的微观结构及形成机理[J].机械工程材料,2014,38(12):42-45. |